Depending on the choice of regulations, applicants should consult the appropriate guide. If you choose to comply with the new regulations, please consult the "New regulations: guide to submitting applications for registration under the Fertilizers Act".
On this page
Fertilizer Safety Section
Canadian Food Inspection Agency
October 2015
Abbreviations
- ATCC
-
American Type Culture Collection
- CFIA
-
Canadian Food Inspection Agency
- CAS #
-
Chemical Abstracts Service number
- CFU
-
Colony Forming Unit
- CBI
-
Confidential Business Information
- PCDD/Fs
-
Dioxins and Furans
- EPA
-
Environmental Protection Agency
- FSS
-
Fertilizer Safety Section
- FzA
-
Fertilizers Act
- FzR
-
Fertilizers Regulations
- GLP
-
Good Laboratory Practice
- IQ
-
Inquiry
- ISO
-
International Organization for Standardization
- LOD
-
Limit of Detection
- LOQ
-
Limit of Quantification
- MSDS / SDS
-
Material Safety Data Sheet / Safety Data Sheet
- ED50 / EC50
-
Median Effective Dose / Median Effective Concentration
- ID50 / IC50
-
Median Infective Dose / Median Inhibition Concentration
- LD50 / LC50
-
Median Lethal Dose / Median Lethal Concentration
- LO(A)EL
-
Lowest Observed (Adverse) Effect Level
- MPN
-
Most Probable Number
- NO(A)EL
-
No Observed (Adverse) Effect Level
- OECD
-
Organisation for Economic Co-operation and Development
- PMRA
-
Pesticide Regulatory Management Agency
- PASO
-
Premarket Application Submissions Office
- QA
-
Quality Assurance
- QC
-
Quality Control
- RoA
-
Results of Analysis
- SDS
-
Service Delivery Standards
- SGN
-
Size Guide Number
- TEQ
-
Toxic Equivalent
- WHMIS
-
Workplace Hazardous Materials Information System
Glossary
- Fertilizer:
-
any substance or mixture of substances, containing nitrogen, phosphorus, potassium or other plant food, manufactured, sold or represented for use as a plant nutrient.
- Infectivity:
-
the ability of a microorganism to cross or evade natural host barriers to infection (to invade and persist in a viable state or multiply within or on an organism, with or without disease manifestation).
- Material Safety Data Sheet / Safety Data Sheet (MSDS / SDS):
-
a comprehensive technical bulletin detailing physicochemical, compositional, first aid, human health and environmental hazard, toxicological, ecological, precautionary, personal protection/exposure control, handling, storage, disposal, firefighting, accidental release, stability and reactivity, transport and regulatory information on a substance or product.
- Microbial Toxin:
-
a substance produced by a microorganism that might have a harmful effect on a host organism, irrespective of the presence of the living microorganism.
- Microorganism:
-
a microscopic living organism that is classified in the Bacteria, Archea, Protista (protozoa and algae), Fungi (including yeasts) and Virus (including virus-like particle or sub-viral particle) taxonomic groups.
- Pathogen:
-
any disease-producing microorganism.
- Pathogenicity:
-
the ability of a microorganism to infect a host, establish itself and multiply there, and subsequently inflict injury or damage that might or might not lead to death.
- Quality Assurance (QA):
-
maintenance of a desired level of quality in a product by means of attention to every stage in the production process to ensure product deficiencies do not arise when the product is being developed.
- Quality Control (QC):
-
maintenance of standards in manufactured products by testing output samples against the specification to ensure the quality of the final product and to identify deficiencies after a product is developed and before it is released.
- Substance:
-
any distinguishable kind of organic or inorganic matter, whether animate or inanimate. This definition includes a pure culture of a microorganism. A blend of microorganisms or a microbial product is a mixture of substances rather than an individual substance.
- Supplement:
-
any substance or mixture of substances, other than a fertilizer, that is manufactured, sold or represented for use in the improvement of the physical condition of soils or to aid plant growth or crop yields.
- Toxicity:
-
the ability of a substance to cause adverse effects on living plants or animals due to its poisonous (toxic) nature.
- Toxigenicity:
-
the ability of a microorganism to produce a toxin.
1. Introduction
1.1 Registrations under the Fertilizers Act
Fertilizers (essential plant nutrients) and supplements (products other than fertilizers that improve the physical condition of the soil or aid plant growth or crop yield) when imported into or sold in Canada are regulated under the authority of the federal Fertilizers Act and Regulations (FzA and FzR) administered by the Canadian Food Inspection Agency (CFIA). Pursuant to the Fertilizers Act and Regulations, all products must be safe with respect to human, animal and plant health and the environment and properly labelled to avoid misrepresentation in the marketplace. Some fertilizers and most supplements require mandatory pre-market assessment and registration prior to importation and sale in Canada. All registrations are valid for 36 months from the date of their issuance. Product proponents wishing to sell or import a registrable product after that date must apply to the CFIA to renew their registration. Furthermore, no changes to the label, chemical composition or ingredients in the product can be made unless the registration is amended accordingly (major or minor amendment). Alternatively, these changes can be made at the time of re-registration. All products regulated under the Fertilizers Act and Regulations may be subject to marketplace monitoring which includes product inspections, sampling and testing as well as label verification. Non-compliant products may be subject to regulatory action including product detention (stop sale) and in cases of serious or repeated non-compliance, prosecution.
1.2 Service delivery standards for registration related submissions
To obtain registration, product proponents must submit an application to the CFIA - all applications must be directed to the Premarket Application Submissions Office (PASO). The file review procedures and associated timeframes (Service Delivery Standards, SDS) for all registration related applications (new registrations, re-registrations, major and minor amendments) are described in Trade Memorandum T-4-122: Service Delivery Standards for Fertilizer and Supplement Registration. The service delivery standards include the actual CFIA review time, the applicant's response time and the queue time since all files are processed in the order they are received. The SDS vary by submission type due to the nature and complexity of the assessment required and allow for up to three review cycles. Please note, that unless there are deficiencies identified in the submission, the file may not require all three reviews and the registration (for example new registration with data) may be issued within 245 days as opposed to 530 days if all three reviews are needed. Therefore, it is critically important that applicants invest the time and effort to familiarize themselves with the registration requirements BEFORE they submit an application to the CFIA.
When deficiencies in the submission are identified at the first review stage the applicants are required to respond to each question posed by the CFIA completely and with sufficient detail to address the deficiency. Partial responses and responses received past the specified timeframe are considered incomplete and the file will be closed. A closed file does not advance to the next review stage and will be returned to the applicant or destroyed. The applicant would then have to re-submit a new package for CFIA's consideration and review. In addition, a file is closed if an applicant discloses substantively new information during the file review process about the product, its composition or manufacturing method, that warrant an additional review or assessment.
1.3 Purpose of the guide
There are a number of documents available on the CFIA website that are intended to increase awareness and understanding of the regulatory requirements for fertilizer and supplements imported into and sold in Canada. The information requirements detailed in this document are specifically designed to assist prospective registrants in preparing complete and well organized submissions to facilitate the file review process and ultimately expedite time to market. This document is accompanied by a Submission Preparation Training that "walks" applicants through the file review process, to offer further guidance to prospective registrants.
1.4 Submission format
The information included in the registration package must be organized in form of sections (tabs) for ease of access and review by multiple CFIA evaluators (toxicologists, microbiologists, agronomists, etc.). All tabs required by product type and/or ingredient must be populated in their entirety. These include: 1) Administrative Forms and Fees; 2) Marketplace Label; 3) Product Specification; 4) Results of Analysis; 5) Safety Rationale and Supplemental Data (as identified in Appendix 1). If the requisite information has already been submitted to the CFIA, the applicants must include a statement to that effect under the appropriate tab and, if applicable, reference all relevant submission control numbers (e.g. 12345IQ) or registration numbers (e.g. 1901001A) previously issued by the CFIA. In addition, bridging rationale substantiating why this information is pertinent to the current submission must also be provided.
While it is permissible for applicants to reference previously submitted information, single complete packages are preferred as they facilitate and expedite file review. It is not acceptable to omit a tab. If a tab or sub-tab is not relevant to the submission, a brief written statement is required (i.e. "This product requires only core product information. As such, all required information has been submitted under Tabs 1, 2 and 3."). Submissions without information or a brief statement under each tab are deemed incomplete and will be closed and returned to the applicant.
1.5 Safety data requirements
To reduce burden on stakeholders and streamline the information required to support registration under the Fertilizers Act and Regulations, the FSS has implemented a graduated approach whereby the extent of the safety data requirements varies depending on the submission type, nature of the product and its risk profile. All applications for registration require the submission of core product information (Safety assessment Level I), some also require results of analysis (Safety assessment Level II) to allow for verification of consistency in production or effectiveness of treatment as well as purity of the final product with respect to contamination levels. Products with a higher or unknown risk profile necessitate a full safety assessment (Safety Assessment Level III), for which scientific rationales, supplemental safety data and/or additional results of analysis are required. The requisite assessment level (I, II or III) is determined based on the product ingredients (both active and inert) and their sources, potential residues, contaminants, and degradation by-products as well as the manufacturing process, use pattern and application rate and frequency. Table 1 shows the three Safety assessment levels and required information by Tab.
Assessment Level | Tab 1 (Administrative Requirements) |
Tab 2 (Labelling Requirements) |
Tab 3 (Product Specification) |
Tab 4 (Results of Analysis ) |
Tab 5 (Safety Rationale and Supplemental Data) |
---|---|---|---|---|---|
I | Check | Check | Check | ||
II | Check | CheckCheck | CheckCheck | CheckCheck | |
III | Check | Check | Check | Check Table Note 1 | Check |
Table Notes
- Table Note 1
-
Level III submissions may require some or all of the results of analysis
A summary of information requirements for a variety of product ingredients can be found in Appendix 2.
Note: The CFIA reserves the right to require additional safety information, data, rationales or results of analysis to support the registration of any product regulated under the Fertilizers Act and Regulations if and when additional safety concerns or questions have been identified during the review of the submission.
In addition to familiarizing themselves with this guide, prospective registrants are encouraged to make use of the Inquiry (IQ) process to seek clarification and obtain guidance on the information requirements specific to their product, prior to submitting an application for registration. Additionally, product proponents may wish to request a Pre-Submission Consultation meeting with the FSS, particularly in the early stages of product development, to obtain guidance, advice, and clarification on the regulatory requirements. The IQ and Pre-Submission Consultation processes can assist product proponents in generating appropriate data and information in support of product registration. Refer to Guidelines for Pre-submission Consultations for Fertilizer and Supplement Products Regulated Under the Fertilizers Act and Regulations for more details.
2. Submission structure and layout
2.1 Tab 1: Administrative forms and fees
This section outlines the core administrative requirements for an application for registration.
2.1.1 - Cover Letter
The applicant is required to state the intent of the submission, thereby ensuring proper submission classification. The following must be indicated in the cover letter:
- Submission type (e.g. new registration, Re-registration, major amendment, minor amendment);
- Safety Assessment level (i.e. I, II or III) required (this will be subject to validation by the CFIA and the categorization may change following the pre-screening stage of the application);
- Reference to submission control number of an inquiry (e.g. 12345IQ) and/or previously granted registration number(s) relevant to the current submission, if applicable;
- Intended end-use of the product (e.g. agriculture, greenhouse, turf, residential lawn, home - indoor, seed inoculation, blending).
2.1.2 - Completed Fertilizer and Supplement Registration Application Form
All sections of the Fertilizer or Supplement Registration Application form must be completely and accurately filled out. As a legal document, the form is required to be completed in its entirety and must exactly match the information stated on the accompanying label. Proponents may reference sections of their submission, if there is insufficient room on the application form. The CFIA reserves the right to return a Fertilizer or Supplement Registration Application to the applicant if the form is deemed incomplete. For more information on how to complete the application form, please refer to the Guidelines to Completing the Fertilizer or Supplement Registration Application Form.
2.1.3 - Designation of Signing Authority (T-4-95) and Declaration of Canadian Agent Form
Before proceeding with the registration of a product, it is necessary to provide the CFIA with signing authority as outlined in: T-4-95 - Signing Authority, Delegated Representatives and Canadian Agents. Signing authority is the means of explicitly informing the CFIA who is authorized to sign a Fertilizer or Supplement Registration Application Form on behalf of the prospective registrant. Signing authority is also used to inform the CFIA who they can correspond with regarding the submission. The CFIA will not divulge any information regarding the submission or discuss its status with any person(s) who does not have a valid signing authority. A corporation may also appoint a person to be a delegated representative. A delegated representative may correspond with the CFIA on matters relating to product registration, re-registration or approval, but may not sign application forms on behalf of the corporation.
It is not mandatory that a registrant/applicant reside in Canada. However, for applicants residing outside of Canada, a Resident Canadian Agent must be designated (by filling out the form in Declaration of Resident Agent Form). The Canadian Agent must co-sign all registration applications (including any re-registrations, amendments, etc.) and may be sent any related notice or correspondence as appropriate. A Canadian Agent must be a person, not a company, and this person must be a permanent resident of Canada. An applicant may have more than one Canadian Agent on file. Designation as the Canadian Agent does not automatically mean the person has a signing authority on the file and a separate statement is required to authorize the CFIA to communicate with the individual regarding the file.
2.1.4 - Registration Fee
In order for the CFIA to process a file, a registration is to be paid as per Part 5 of CFIA's Fees notice.
- Fees described in the CFIA's Fees Notice apply to applications made under the Fertilizers Act to:
- register;
- re-register;
- amend a registration; or
- assess the safety of a product.
- In cases when the applicant requests a safety assessment only (no registration) the registration fee is not charged and the safety assessment fee is payable when the request is submitted.
In order to ensure consistency in the collection of fees and predictability for regulated parties, the safety fees are applied to all Level II and Level III safety assessments as defined in this guide.
Product type | Registration fees | Safety fees |
---|---|---|
Major Amendment (AM) Table Note 2 Table Note 4 | Check | |
Minor Amendment (MA) Table Note 3 | Check | |
New Registration (NR) Level I | Check | |
New Registration (NR) Level II | Check | Check |
New Registration (NR) Level III | Check | Check |
New Registration (NR) me-too | Check | |
Reregistration (RR) Table Note 2 | Check |
Table Notes
- Table note 2
-
Safety fees are charged for a re-registration application or a major amendment only in cases where substantive changes to the product formulation are made, thereby triggering a safety assessment, which will be determined by a CFIA evaluator at 1st response.
- Table Note 3
-
Minor amendment: an application to amend a registration outside of the re-registration process with respect to one or more of the following: (i) the name or address of the registrant and/or manufacturer; (ii) the colour or format of the label; (iii) the product name and/or brand; (iv) the declaration of net weight.
- Table Note 4
-
Major amendment: an application to amend a registration outside of the re-registration process, where changes lie outside the scope of a minor amendment as defined in table note 3.
2.2 Tab 2: Proposed marketplace label
According to the Fertilizers Act and Regulations every package containing a fertilizer or supplement must have a label, a copy of which must be submitted with the application for registration. The CFIA will accept text versions of the label during the initial review stages, but will not register the product without reviewing the final marketplace label. The CFIA requires that any hazard or precautionary statements and personal protective equipment requirements that appear on the (M)SDS or their equivalents be incorporated into the product labels. If these are contained within the WHIMS (Workplace Hazardous Materials Information System) box/portion of the label, they need not be duplicated. Additional precautionary statements and/or protective equipment requirements may be requested by the CFIA even if they do not appear on the (M)SDS. All text appearing on a label must be legible in English or French or in both English and French.
The label shall not contain:
- any incorrect or misleading information or mark; or
- a brand or name that would tend to deceive or mislead a purchaser with respect to the identity of the product as a fertilizer or supplement or its safe use.
The following is required on product labels:
2.2.1 - Fertilizer
- the name and address of the manufacturer of the fertilizer or of the registrant or, in the case of a fertilizer that is not registered, the name and address of the person who caused the fertilizer to be packaged;
- the brand of the fertilizer, if any;
- the name of the fertilizer;
- the registration number of the fertilizer, where applicable;
- the guaranteed analysis (expressed in percent);
- the directions for use;
- the weight of the fertilizer;
- where the fertilizers with the exception of specialty fertilizers that guarantee boron, copper, iron, manganese, molybdenum or zinc, the following cautionary statement:
"Caution: This fertilizer contains (specify name of lesser plant nutrient) and should be used only as recommended. It may prove harmful when misused."; - Boron is a Category 1B reproductive toxicant. All fertilizers with a Boron content greater than or equal to 0.3% of the final product require the following statement on the product label or its equivalent: "May damage fertility or the unborn child".
- where a fertilizer contains corn gluten meal or iron sulphate represented for use on lawns (home and garden) and has been approved for use with a fertilizer by the PMRA, appropriate precautionary statements (refer to Appendix 9);
- in the case of a fertilizer that is or contains any prohibited material, as defined in subsection 162(1) of the Health of Animals Regulations, other than a rendered fat, conspicuous statements written legibly and indelibly in both official languages that indicate that:
- feeding the product to cattle, sheep, deer or other ruminants is illegal and subject to fines or other punishment under the Health of Animals Act,
- the product is not to be used on pasture land or other grazing areas for ruminants,
- the product is not to be ingested, and
- a person should wash his or her hands after the person uses the product;
- the lot number of the fertilizer, unless the fertilizer is a customer-formula fertilizer; and
- if sold in bulk, all labelling information is required on the shipping bill or on a statement accompanying the shipment.
2.2.2 - Supplement
- the name and address of the manufacturer of the supplement or the name and address of the registrant or, in the case of a supplement that is not registered, the name and address of the person who caused the supplement to be packaged;
- the name of the supplement;
- the weight of the supplement;
- the directions for use of the supplement;
- the lot number of the supplement;
- the guaranteed analysis (as applicable):
- the minimum amount of the active ingredient in the supplement, expressed in per cent;
- the genus and species of viable microorganisms; and
- the minimum number of viable cells of each microorganism per gram of product, expressed, for example, in CFU or spores per gram;
- in the case of a supplement in which the active ingredient may deteriorate, the date beyond which the supplement is not intended for use;
- where the supplement contains viable microorganisms, the label may require cautionary statements and/or recommend personal protective equipment, in order to minimize dermal/respiratory sensitization/irritation potential.
- in the case of packages of pre-inoculated or coated pre-inoculated seed, the minimum guarantee of the inoculant or the following statement "The product is treated with (species name or genus of the active microorganism(s)) inoculum.";
- where the supplement is represented to contain supplemental metal, such as cobalt, the following cautionary statement:
"Caution: This fertilizer contains (specify name of the supplemental metal) and should be used only as recommended. It may prove harmful when misused."; - in the case of a supplement that is or contains prohibited material, as defined in subsection 162(1) of the Health of Animals Regulations, conspicuous statements written legibly and indelibly in both official languages that indicate that:
- feeding the product to cattle, sheep, deer or other ruminants is illegal and subject to fines or other punishment under the Health of Animals Act,
- the product is not to be used on pasture land or other grazing areas for ruminants,
- the product is not to be ingested, and
- a person should wash his or her hands after the person uses the product;
- the registration number of the supplement if the supplement is required to be registered; and
- if sold in bulk, all labelling information is required on the shipping bill or on a statement accompanying the shipment.
2.3 Tab 3: Product specification
All ingredients in the product (both active and inert) and their sources must be identified and listed under this tab. In addition, a detailed description of the manufacturing process preferably in the form of a flow chart is required together with all relevant quality control/assurance procedures used to ensure consistency in production and purity of the final product. This information is the minimum necessary for CFIA to conduct a preliminary assessment of the product and determine if additional information is required. It is intended for CFIA evaluators only and it is considered and treated as Confidential Business Information (CBI). CBI shall not be divulged or released without explicit authorization (in writing) of the registrant. If the registrant has or anticipates any difficulties in obtaining this information (due to its proprietary nature) it may be submitted by the distributor or manufacturer directly to the CFIA.
2.3.1 - List of Ingredients
2.3.1.1 - Input materials
For all materials used in the production of a registrable fertilizer or supplement, except microbial inocula described in section (2.3.1.2), the following information is required:
- Name of the material;
- Chemical Abstracts Service number (CAS #, if available);
- Manufacturer;
- Country of origin;
- Source: e.g. manufactured (e.g. dyes, chelators), harvested (e.g. seaweed, straw, yucca), mined (e.g. ores), by-product (e.g. baghouse/electrostatic dust, klinker, slag, electrolysis, ash), recycled organics* (e.g. source separated organics, compost, biosolids, pulp and paper), synthesized (describe the chemical reaction and any residuals and reaction by-products);
- Manufacturing/purification processes of the ingredient, if applicable;
- Concentration of the material in the final product;
- Purpose of the material; and
- Material Safety Data Sheets (MSDS) or Safety Data Sheets (SDS) which serve as basis for preliminary safety evaluation, identifying points (such as possible contaminants) which may need to be examined in greater detail. An (M)SDS should also provide a detailed explanation of precautions and protective measures. The Workplace Hazardous Materials Information System (WHMIS) provides criteria for developing an (M)SDS.
* Recycled organics are required to indicate their inputs or feedstocks
Multiple sources of an ingredient may be identified at the time of product registration and used interchangeably during the manufacture of the product. Note: any changes to the ingredients, their sources or their supplier(s) or changes to the formulation after registration require a major amendment.
2.3.1.2 - Microbial Inocula
For products that contain naturally occurring viable microorganism(s) the following information is required:
- Purpose of the microbial strain in the supplement;
- Taxonomic identification of the microorganism to the genus and species level; subspecies, and strain information may also be required depending on the nature of the microorganism),
- Analytical results (including criteria and raw data) substantiating the taxonomic ID and classification;
- Relationship to known pathogens (e.g. phylogenetic trees);
- Origin of the microorganism (when, where and from which material it was isolated) if it is an environmental isolate; or the strain bank accession numbers if the strain has been deposited in a recognized culture collection, e.g., American Type Culture Collection (ATCC) or other.
Strong and defensible taxonomic identification, preferably to the strain level, is important for the hazard characterization of the microorganism. The choice of methods for microbial identification is at the discretion of the applicant. However, the CFIA recommends that applicants adopt an integrated polyphasic approach that includes phenotypic analysis (e.g. analysis of morphological traits or biochemical characteristics) along with molecular tools (e.g. DNA, RNA or protein based methods), to accurately identify the microorganism. The strengths and weaknesses of the various identification methods should be taken into consideration, such that the methods chosen complement each other to result in a conclusive and definitive identification of the microorganism, and allow for clear differentiation of the organism from any closely related pathogenic and/or toxigenic species and strains. Please consult Identification and taxonomic classification of microorganism(s) represented for use as supplements under the Fertilizers Act for further detail.
Additionally for microorganisms modified by molecular biological techniques the following information is required:
- Flow diagram representing the genetic modification process including:
- the map of the construct inserted in the host,
- location (chromosomal or plasmid),
- copy number,
- cloning vector(s) used,
- promoter sequences,
- selectable marker genes including any antibiotic resistance genes.
- Detailed description of the gene product(s), their properties and functions;
- Description of the metabolic pathways altered by the insertion;
- Unintended effects on gene expression (down-regulation or up-regulation of other genes);
- Stability of the inserted genetic material;
- Horizontal gene transfer potential: capacity to transfer the genetic material between the organism and non-target species, the mechanisms of possible transfer (transformation, transduction or conjugation) and the elements involved (plasmids, bacteriophages, integrative conjugative elements, transposons, insertion sequences, integrons, gene cassettes and genomic islands);
- Procedures and tests to detect and quantify the modified microorganisms.
Substantiation of the purity of the inoculum is also required and includes:
- A description of the quality control parameters used to monitor, identity and purify the microorganism from the seed stock (primary inoculum), and the company name and address that keep the seed stock;
- The manufacturing process and quality control parameters used to monitor the identity and purity of the final inoculum (used as an ingredient in the final product, generally mixed with inert ingredients); and
- (M)SDS of the inoculum, if available.
2.3.1.3 - Composition of the Final Product
- The identity and relative proportions as weight/weight percentages (totalling 100%) must be provided for all ingredients present in the final product including all active and inert ingredients, contaminants, residuals, reaction by-products and degradation products;
The input materials may be the same as the final product constituents providing there are no chemical reaction(s) or metabolic by-products generated during the manufacture/storage of the final product prior to sale and no growth of new microorganism(s) is taking place. - (M)SDS, if available.
2.3.2 - Method of Manufacture
A description of the manufacturing process of the final product accompanied by a flowchart used as an overview of the process to determine if there is any potential for secondary reactions, formation of by-products and/or microbial contamination. This description must specify each production step, including point of feedstock incorporation and its proportion by weight and associated conditions, such as temperature, pressure, time, and processing equipment.
2.3.3 - Quality Assurance and Quality Control Procedures
In order to substantiate consistency in production and safety of the final product, proponents are required to provide the following details relating to Quality Assurance (QA) and Quality Control (QC) procedures used during manufacture process:
- Substantiation of the conformance of raw materials to specifications and standards (with analysis or accreditation when applicable);
- Indication of material(s) being tested (e.g. raw, intermediary or final product);
- Specification of analyses and sensitivity of test methods (limits of detection and/or limits of quantification);
- Identification of "pass" criteria;
- Testing frequency (e.g. per batch or unit time) and point of sampling during production;
- Monitoring of manufacturing conditions (e.g. time, pressure, moisture content); and
- Fate of noncompliant batches/lots (e.g. reprocessing, disposal).
2.3.4 - Physical Characteristics of the Final Product
For example: granular, liquid, pH, colour, odor, size guide number (SGN).
2.4 Tab 4: Results of analysis
The results of analysis required in support of a registration vary depending on product type and the source of ingredients. Examples of ingredient-specific results of analysis that are required to be included in a submission are provided in Appendix 2. The safety standards and limits for trace metals, dioxins and furans and indicator organisms (Salmonella and Fecal Coliform) used by the CFIA to assess product safety and efficiency of treatment or processing are outlined in Appendix 3. The upper tolerances around guarantees for fertilizers represented to contain micronutrients are also outlined in Appendix 3.
Product samples must be taken at intervals enabling assessment of the consistency in production (e.g. at regular time intervals, upon receipt of raw materials, per lot/batch, etc.). Applicants are required to indicate the number of batches produced annually. All results of analyses submitted to the CFIA must be printed on laboratory letterhead, bear the signature of the analyst, indicate sample preparation method(s) the test method(s) used together with limits of Quantitation (LOQ) and/or limits of detection (LOD). The results of analysis must also identify the body that certified/accredited the laboratory. To facilitate file review, results of analysis are to be accompanied by a table with all of the following column headings, identifying for each analysis and sample:
- name of product and/or constituent material (in full, no abbreviations);
- laboratory sample identification number;
- manufacturing/sampling date; and
- type of analysis (e.g. metals/micronutrients, dioxins and furans, indicator organisms).
2.4.1 - Metals
To demonstrate conformance with the trace metal standards, proponents are required to provide results of analyses for the 11 metals of concern: As, Cd, Co, Cu, Cr, Hg, Mo, Ni, Pb, Se, and Zn. Lime products manufactured using industrial by-products, such as cement kiln dust and cement clinkers, require Thallium (Tl) and Vanadium (V) results of analysis in addition to the previously indicated 11 metals of concern. The number of metal analyses that are required at the time of new registration or re-registration depends on the total number of batches/lots of product manufactured within a three (3) year interval preceding the submission of an application for a new or re-registration (see Table 2). Products produced via a continuous process require 6 sets of analysis evenly spread over the three (3) year interval preceding the submission. Requirements for metals analyses (including the number of analyses needed to support registration) for fertilizers and supplements that are not yet in mass production are strongly dependent on the inputs, their sources and application rates. They are therefore determined on a case-by-case basis. In order to determine the sampling requirements for products that are not yet being manufactured, prospective registrants are encouraged to make use of the IQ process prior to submitting an application for registration.
# of Batches/Lots produced within the 3 years preceding the submission | # of Sample analyses required |
---|---|
1 | 1 |
2 to 4 | 2 |
5 to 9 | 3 |
10 to 16 | 4 |
17 to 25 | 5 |
26+ Schedule to be provided by stakeholder and approved by the CFIA | To be determined |
Analytical methods currently used for metal testing by the CFIA laboratories are available on request from the Food Safety Science Services Division (FSSSD) Laboratory Coordination CFIA.LCD-DCL.ACIA@inspection.gc.ca. Please be advised that the CFIA is not responsible to notify and/or distribute any future amendments or versions of the documents. The protocols are fit for a specific defined use and intended for CFIA regulatory testing only – the CFIA is not responsible for the use of this protocol for any other purpose. Neither the CFIA nor the Government of Canada is liable for any results obtained through the use of these protocols or procedures.
2.4.2 - Dioxins and Furans
To demonstrate compliance with the CFIA Fertilizer Dioxin and Furan Standards, proponents must provide one (1) set of TEQ dioxins and furans analyses (see Table 4, Appendix 3). Note: Not all level II safety assessments require the submission of dioxin and furan analyses.
2.4.3 - Indicator Organisms
Salmonella and Faecal coliforms are currently used by the CFIA as indicators of pathogen contamination and effectiveness of the treatment process. To demonstrate compliance with the CFIA requirements, proponents must provide four (4) sets of result of analyses from four different lots/batches of the final product for faecal coliform and Salmonella. Samples must be taken at intervals of at least two weeks for continuous or semi-continuous batches, or at intervals that correspond to the actual batch manufacture (see Table 5, Appendix 3).
2.4.4 - Upper tolerances for nutrient guarantees for fertilizers represented to contain micronutrients
To demonstrate compliance with the CFIA upper tolerances for fertilizers represented to contain micronutrients, proponents are required to provide results of analysis for guaranteed micronutrients in addition to the results of analysis for the reportable metals (As, Cd, Co, Cu, Cr, Hg, Mo, Ni, Pb, Se, Zn). The analyses are required both at the time of registration and re-registration to ensure that the actual content of the nutrient in the product does not exceed the guarantee by an amount that is higher than the allowable tolerance (see Table 6, Appendix 3). The number of analyses required will be based on the number of batches produced as per the current policy - for details please refer to Table 2 above.
2.5 Tab 5: Safety rationale and supplemental data
Product safety assessments are conducted using the universal four (4) step risk assessment framework that is also employed by other CFIA programs (e.g. plant, animal, food), sister government departments or Agencies (e.g. Health Canada, Environment Canada, Pesticide Regulatory Management Agency (PMRA), and international counterparts (e.g. US Environmental Protection Agency (EPA)). The four steps of the framework consist of: hazard identification, dose-response assessment (hazard characterization), exposure assessment and risk characterization.
- Hazard identification is a determination of the adverse human health and environmental effects.
- Dose-response assessment is a quantification of the relationship between administered/received dose and biological response of an individual or population.
- Exposure assessment predicts the anticipated level of human and organism contact and/or uptake and environmental media concentrations that arise as a result of product use.
- Risk assessment is a deterministic or probabilistic estimate of the incidence of the adverse human and ecological effects on the basis of the hazard characterization and what is known about exposure; this is the basic risk assessment paradigm (Risk = Hazard × Exposure).
The information detailed in this section is required to substantiate the safety of a product with respect to human, plant, and animal health and the environment when the product is used as directed. Based on the assessment, additional information may be requested by the CFIA. The safety rationales and supplemental data are only required for level III full safety assessments and are determined based on the risk profile of the product. This Tab has been broken down into three (3) sections: Toxicological Risk Profile; Microbial Risk Profile; and References and Supplemental Documentation. The CFIA strongly recommends that applicants seek assistance/advice from scientific professionals with an expertise in human and environmental toxicology and/or microbiology to assist in preparing documentation required under this tab.
Where there are reasonable scientific grounds to believe that an information requirement identified in this tab is neither necessary, nor applicable to the safety assessment of a product/ingredient, a waiver from the information requirement or elements of it may be requested, and must be accompanied by a sound scientific rationale.
2.5.1 - Toxicological Risk Profile
2.5.1.1 - Toxicological Hazard Characterization
All fields of the table found in Appendix 4 must be completed for ingredients that warrant a level III safety assessment (i.e. for products or ingredients that do not have a well-established history of safe use in fertilizers and supplements). The alternative to this requirement is to provide a literature-supported scientific rationale explaining why elements of the table are either not applicable or relevant to the ingredient. If other hazard endpoints (e.g. allergenicity), route-specific hazards (e.g. pulmonary carcinogenicity with chronic inhalation exposure) or species-specific hazards (e.g. avian toxicity) are known to the applicant, it is their responsibility to identify them. Additional information may be required by the CFIA depending on risks identified.
Toxicological hazard characterization may be based on information found in published peer-reviewed scientific literature, international regulatory databases, in vitro and in vivotoxicity testing/studies and, in the absence of experimental data, modelling. Information pertaining to a similar substance may be submitted (surrogate data). This requires a bridging rationale demonstrating similarity between the substances of interest and its surrogate including all relevant characteristics (physical, chemical, or toxicological).
Where an ingredient has:
- high acute toxicity (LD50 ≤ 500mg/kg, ≤ 1 500mg/m3),
- subchronic toxicity (NO(A)EL ≤ 30mg/kg bw/d; LO(A)EL ≤ 90mg/kg bw/d),
- or chronic toxicity (NO(A)EL ≤ 10mg/kg bw/d; LO(A)EL ≤ 30mg/kg bw/d),
- exhibits carcinogenicity, clastogenicity, mutagenicity, reproductive or developmental toxicity, teratogenicity or endocrine disruption (a positive result),
- or is of high acute aquatic toxicity (lowest EC50/LC50<0.1ppm),
it is considered a high hazard ingredient. For high hazard ingredients (i.e. those that meet any of the Hazard Criteria identified in Appendix 4) the Toxicological Exposure and Risk Assessment must be conducted (as detailed in sub-tab 2.5.1.2 and 2.5.1.3). Ingredients that do not meet any of the hazard criteria do not require an Exposure Assessment or Risk Assessment and completion of sub-tab 2.5.1.2 and 2.5.1.3 is not mandatory. Appendix 10 provides a list of useful information resources to aid in the hazard determination.
2.5.1.2 - Toxicological Exposure Assessment
Applicants must populate all fields of the table found in Appendix 5 for all constituent materials (active and inert), residuals, contaminants and degradation products for which a high hazard level has been identified, as per the endpoint-specific Hazard Criteria found in Appendix 4. Both direct routes of exposure (occupational mixer, loader, applicator/user) and indirect routes of exposure (by-stander, groundwater, food or feed crop residue, contaminated soil contact and consumption) must be addressed. The choice of appropriate or relevant routes of exposure is based on the intended use pattern of the product (e.g. agricultural field use vs. potting mixes; ornamental plant species vs. food crops), frequency and rates of application as well as the physicochemical properties of the product and its constituents. These are important factors in determining human, animal, non-target plant and environmental exposure scenarios and must be identified in Appendix 5. Applicants must consider worst-case exposure scenarios. Label statements intended to limit exposures such as recommendations for protective equipment to be used, safe handling and disposal procedures, precautionary statements and use pattern restrictions (e.g. do not use on food crops or grazing lands) as well as post-entry intervals (if applicable) should be integrated in the estimates of human and environmental exposure. The CFIA considers the custom-applicator scenario as the worst-case frequency of occupational exposure.
2.5.1.3 - Toxicological Risk Assessment
Applicants must generate estimates of risk (to be populated in Appendix 5) by combining the hazard and exposure assessments for each high hazard ingredient under all relevant exposure scenarios characterized in sub-tab 2.5.1.2. The CFIA will review and validate the risk estimate(s) derived by the applicant. Additional information/test data may be required in order to refine the exposure and hazard assessments and/or require mitigation measures such as protective equipment to be used, safe handling and disposal procedures, precautionary statements, use pattern restrictions (e.g. food vs. non-food crop) and any post-entry intervals, if applicable to facilitate safe use of the product.
2.5.2 - Microbial Risk Profile
2.5.2.1 - Microbial Hazard Assessment
A hazard assessment characterizes the microorganism and identifies the potential adverse effects (i.e., pathogenicity/toxicity, sensitization, toxigenicity) towards humans, animals and plants, and the environment. The hazards may be posed by the microorganism itself, its metabolites/toxins or its genetic material.
Source of hazard information include test data, a review of case reports and analytical studies from scientific literature, and research investigations (completed or ongoing). Hazard information considered in the assessment may be for the specific microorganism being assessed, or a suitable surrogate, if there is insufficient information on the specific microorganism and the choice of surrogate is supported by a sound scientific rationale. Factors affecting the severity (degree) of hazard may be strain specific and therefore the assessment must address the factors known or suspected to be produced by the strain, as well as those known or suspected to be produced by other strains of the species (or genus). The severity of hazard may also be affected by the life stage of the organism. For this reason, all stages of the life cycle of the microorganism and their potential effects must be considered.
Ideally, test/study data are used to evaluate the potential adverse effects of the specific microorganism being assessed. Testing typically starts with a maximum hazard dose (maximum label dose/rate). If adverse effects are reported at this dose, a range of lesser doses may be used to establish a dose-response relationship, and ideally to identify an appropriate statistical endpoint, such as median infective, effective or lethal dose or concentration (ID50/IC50, ED50/EC50, LD50/LC50) (Environment Canada, EPS 1/RM/46, March 2005). Recommended methodology for testing the pathogenicity/toxicity of microorganisms on human, animals and plants are available in the "Guidance document for testing the pathogenicity and toxicity of new microbial substances to aquatic and terrestrial organisms" (Environment Canada, Report EPS 1/RM/44, March 2004). Appendix 11 describes the documents referenced in this section and additional useful information resources. A study report should be prepared for each study. The OECD's Principles of Good Laboratory Practice (GLP) include guidance on reporting study results (OECD; 1998a). The extent of compliance with OECD's Principles of Good Laboratory Practice should be indicated.
Appendix 6 highlights the data required for microbial hazard characterization. Applicants must provide the CFIA with information regarding each row of the table, with appropriate reference(s), in a separate document entitled "Technical information - Hazard Characterization". We recommend that the applicant uses Appendix 6 as a checklist to assist in providing all relevant information that is required. The information presented should be referenced, and a copy of each referenced publication/documentation or analytical/study report must be provided in the submission.
2.5.2.2 - Microbial Exposure Assessment
Information considered in the exposure assessment may be for the specific microorganism being assessed, or a suitable surrogate, if there is insufficient information on the specific microorganism and the choice of surrogate is supported by a sound scientific rationale.
An exposure assessment identifies the mechanisms by which a microorganism is introduced into a receiving environment, considers its environmental expression and fate, and estimates the likelihood, magnitude, frequency, duration, and/or extent of human and environmental exposure. Exposure to the microorganism may be direct (e.g., through contact with the product) or indirect. Indirect exposure assessment considers how the microorganism is released into the environment through known, proposed or predicted uses, and the environmental fate of the microorganism, its genetic material, toxins and metabolites.
Appendix 7 highlights the factors that need to be addressed in order to characterize the exposure to the microorganism. Applicants must provide the CFIA with information regarding each row of the table, with appropriate reference(s), in a separate document entitled "Technical information - Exposure Characterization". We recommend that the applicant uses Appendix 7 as a checklist to assist in providing all relevant information that is required.
2.5.2.3 - Microbial Risk Assessment
The risk assessment conclusion is based on the hazard, and on what is known about the exposure. Considerations for classification of microbial hazard severity and exposure level are summarized in Appendix 8. Where appropriate, any preventative risk mitigation measures such as protective equipment to be used, safe handling and disposal procedures, precautionary statements and use pattern restrictions (e.g. do not use on food crops or grazing lands) as well as post-entry intervals maybe required to minimize worker and environmental exposures.
2.5.3 - References and Supplemental Documentation
All published information used to fulfill the requirements under Tab 5 must be cited in-text (author/source, year) and also provided in a list of references under this sub-tab. Each document must be properly referenced (authors, document name, source, date and page numbers).
Also, copies of all published information referenced under Tab 5 and analytical results used or mentioned in Tab 4 and Tab 5 must be provided under this sub-tab. All models or modelling software employed in support of the safety rationale must be cited in-text (model, version) and must also be provided in the list of references under this tab.
Appendices
Appendix 1: Mandatory list of tabs and sub-tabs
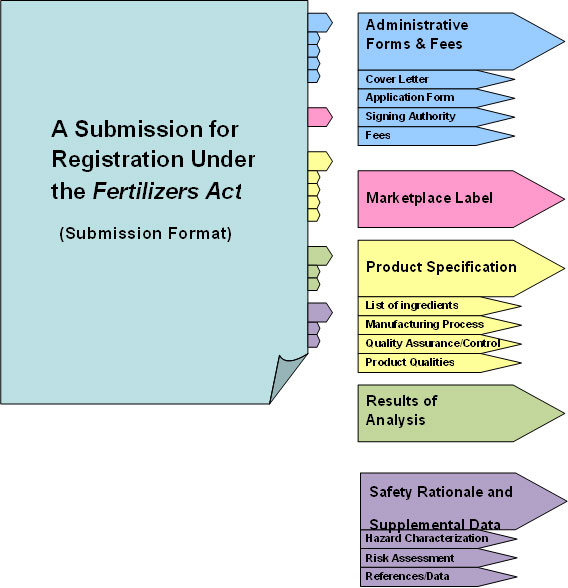
Long Description: This image represents the mandatory format for submitting an application for registration under the Fertilizers Act.
This image includes a structured list of tabs and sub-tabs to assist applicants in preparing well organized submissions. The entitled tabs and sub-tabs include:
- Administrative Forms and Fees
- Cover Letter
- Application Form
- Signing Authority
- Fees
- Marketplace Label
- Product Specifications
- List of ingredients
- Manufacturing Process
- Quality Assurance/Control
- Product Qualities
- Results of Analysis
- Safety Rationale and Supplemental Data
- Hazard Characterization
- Risk Assessment
- References/Data
Safety assessment levels and required sections by TAB
Safety Assessment Level I: Complete Tabs 1-3
Safety Assessment Level II: Complete Tabs 1-4
Safety Assessment Level III: Complete Tabs 1-5
Figure 1: Format of the submission. All Tabs are mandatory and omitting any Tabs will result in the application for registration being rejected / returned to applicant during the first response stage. Please adhere to the headings of each tab as identified in the guide.
Appendix 2: Product ingredients and associated safety data requirements
The presence of an active or inert ingredient in the product may trigger additional safety requirements. If a product includes one or many bolded materials from the table below, it requires registration prior to import or sale in Canada (with the exception of treated seeds or potting soils that contain registered "bolded" ingredients). All products comprising or containing industrial by-products or recycled organic materials require Tab 4 (Results of Analysis).
Tabs 1, 2, 3 | Tab 4 - Metals | Tab 4 - Dioxins Furans | Tab 4 - Indicator Organisms | Tab 5 | |
---|---|---|---|---|---|
Indole-3-butyric acid (IBA) at a concentration not exceeding 1% of the product excluding products for spray application | Check | ||||
VAMs (Vesicular Arbuscular Myccorhizae) provided the species is substantially equivalent/representative of VAM group | Check | ||||
Rhizobia (species of the genera Rhizobium, Bradyrhizobium, Mesorhizobium and Sinorhizobium) provided the species is substantially equivalent/representative of the rhizobia group, and is not genetically modified. | Check | ||||
Bacillus subtilis provided the strain is representative of the species, is not genetically modified and does not produce any human enterotoxin. | Check |
Tabs 1, 2, 3 | Tab 4 - Metals | Tab 4 - Dioxins Furans | Tab 4 - Indicator Organisms | Tab 5 | |
---|---|---|---|---|---|
Mineral derived nutrients (require registration if single ingredient, for farm use and not on Schedule II) | Check | Check | Table Note 3 | ||
Biochar | Check | Check | Check | ||
Micronutrients Table Note 4 | Check | Check | Table Note 3 | ||
Humic and Fulvic Acids | Check | Check | Check Table Note 6 | ||
Plant extracts and residues | Check | Check | Check | ||
Seaweed | Check | Check | Check | ||
Farm Fertilizers containing Cement Kiln Dust | Check | Check Table Note 5 | Check | ||
Farm Fertilizers containing Compost | Check | Check | Check | ||
Farm Fertilizers containing Meals | Check | Check | Check | ||
Farm Fertilizers containing Processed sewage including composts thereof | Check | Check | Check | Check | |
Farm Fertilizers containing Pulp and paper sludge | Check | Check | Check | Check | |
Farm Fertilizers containing Wood ash | Check | Check | Check | ||
Farm Fertilizers containing Organic waste | Check | Check | Check | ||
Silica | Check | Check | |||
Basalt | Check | Check | |||
Fish fertilizer | Check | Check | Check |
Table Notes
- Table note 3
-
source dependent.
- Table Note 4
-
micronutrients only require registration when they are not combined with any other type of nutrient (i.e. nitrogen, phosphorous, or potassium), with the exception of chelator derived nitrogen.
- Table Note 5
-
require Thallium and Vanadium testing in addition to the 11 standard metal analytes.
- Table Note 6
-
non-coal derived humic and fulvic acids requires indicator organisms analysis.
Tabs 1, 2, 3 | Tab 4 - Metals | Tab 4 - Dioxins Furans | Tab 4 - Indicator Organisms | Tab 5 | |
---|---|---|---|---|---|
Polymer coated fertilizers Table Note 7 | Check | Check | |||
Polymeric soil stabilizers | Check | Check | |||
Wetting agents and surfactants | Check | Check | |||
Nano-encapsulated fertilizers and nano-materials Table Note 8 | Check | Check | |||
Plant growth regulators and Plant signalling compounds (e.g. Gibberellin, Cytokines, NAA, LCOs, Salicylic Acid, Chitosan, Hesperetin, Naringenin) other than Level I IBA as described above | Check | Check | |||
Registrable supplement(s) that would themselves require a full safety data package, blended with fertilizer. | Check | Table Note 9 | Table Note 9 | Table Note 9 | Check |
Inoculant extenders sold with an unregistered inoculant | Check | Check | Check | ||
Viable microorganism(s) other than those described in Level I | Check | Check | Check | ||
Metabolites of organism(s) | Check | Check | Check |
Table Notes
- Table Note 7
-
polymer coated fertilizers require safety assessment even if exempt from registration.
- Table Note 8
-
all products in part or in whole comprised of nano-materials require full safety assessment.
- Table note 9
-
Basic Results of Analysis required depending on the ingredients.
Note: this does not constitute a comprehensive list of product /ingredient - specific requirements.
Appendix 3: Metals, dioxins/furans standards and maximum acceptable level of indicator organisms in fertilizers and supplements
Metals Standards
The metals of concern include arsenic (As), cadmium (Cd), chromium (Cr), cobalt (Co), copper (Cu), mercury (Hg), molybdenum (Mo), nickel (Ni), lead (Pb), selenium (Se) and zinc (Zn). Accumulation of these metals in soil over the long term may lead to plant, animal, environmental or human toxicity. The maximum concentration of metals permitted in a product depends on the application rate of the product.
Metals standards are predicated on the maximum acceptable cumulative addition to soils over a 45 year time period, as opposed to the actual concentration of the metal in the product. The application rate of a product is a crucial element in determining acceptable product metal concentrations. The 45 year cumulative application approach is intended to account for the persistence of metals in the environment which ultimately determines the level of contamination and thus, long term impacts.
The maximum acceptable product metal concentration (in mg metal/kg product) is calculated for each metal using the CFIA standards for maximum acceptable 45-year cumulative metal additions to soil (identified in Table 3) and the product's maximum recommended annual application rate as follows:

Description
The maximum acceptable concentration of a metal of concern in a product is equal to one million times the maximum acceptable cumulative addition of the metal of concern to soil over 45 years divided by the product's annual application rate times 45.
All fertilizers and supplements, including processed sewage, composts and other by-products are required to meet the standards for maximum acceptable cumulative metal additions to soil. Certain metals such as copper (Cu), molybdenum (Mo) and zinc (Zn) are also essential plant nutrients. Products represented to contain (i.e. guarantee) Cu, Mo and Zn that are used to treat a specific nutrient deficiency are not required to have an application rate specified on the label, rather the label states that the application rate is to be based on a soil or tissue test. In those instances concentrations of the metal may exceed the metal standard (due to limited frequency of application) and the 95th percentile of the provincially recommended agronomic application rate for the guaranteed nutrient is used in the calculations. These products must still meet the prescribed labelling standards including representation of the element as a plant nutrient, the associated guaranteed analysis and appropriate precautionary statements.
Note: The application rate and the metal concentration must be presented on the same basis (i.e. both dry weight or both as is).
Metal | Maximum Acceptable Cumulative Metal Additions to Soil over 45 Years (kg metal/ha) |
Examples of Maximum Acceptable Product Metal Concentration Based on Annual Application Rates (mg metal/kg product) 4400 kg/ha - yr |
Examples of Maximum Acceptable Product Metal Concentration Based on Annual Application Rates (mg metal/kg product) 2000 kg/ha - yr |
Examples of Maximum Acceptable Product Metal Concentration Based on Annual Application Rates (mg metal/kg product) 500 kg/ha - yr |
---|---|---|---|---|
Arsenic (As) | 15 | 75 | 166 | 666 |
Cadmium (Cd) | 4 | 20 | 44 | 177 |
Chromium (Cr) | 210 | 1060 | 2333 | 9333 |
Cobalt (Co) | 30 | 151 | 333 | 1333 |
Copper (Cu) | 150 | 757 | 1666 | 6666 |
Mercury (Hg) | 1 | 5 | 11 | 44 |
Molybdenum (Mo) | 4 | 20 | 44 | 177 |
Nickel (Ni) | 36 | 181 | 400 | 1600 |
Lead (Pb) | 100 | 505 | 1111 | 4444 |
Selenium (Se) | 2.8 | 14 | 31 | 124 |
Thallium (Tl) Table Note 10 | 1 | 5 | 11 | 44 |
Vanadium (V) Table Note 10 | 130 | 656 | 1444 | 5777 |
Zinc (Zn) | 370 | 1868 | 4111 | 16444 |
Table Notes
- Table note 10
-
Note that not all products require results of analysis for Thallium and Vanadium. These are an example of additional results that may be requested based on product or material type, on a case-by-case basis.
Note: The Canadian Council of Ministers of the Environment (CCME), Bureau de normalisation du Québec (BNQ) and many provinces also have guidelines for metals in soils, or in sludge, compost, and other products that are land applied. We recommend that you contact your provincial government to obtain additional information.
Including a guarantee for Selenium or Cobalt makes the product a registrable supplement because these are not nutrients essential for all plant species.
A compliance verification tool, an excel spreadsheet that automates metal standard calculations, is available upon request from paso-bpdpm@inspection.gc.ca. It is intended to assist manufacturers/proponents and CFIA inspectors in determining conformance of the final product with the standards.
Dioxins/Furans Standard
The CFIA standard for maximum acceptable cumulative addition to soils of polychlorinated dibenzo-p- dioxins (dioxins; PCDD) and polychlorinated dibenzofurans (furans; PCDF) is 5.355 mg TEQ/ha over 45 years (where TEQ = Toxic Equivalency Quotient). Like the CFIA metals standards, the application rate of a product is a crucial element in determining acceptable product dioxins/furans concentrations and the 45 year cumulative application approach is employed to account for environmental persistence and long-term impacts.
The maximum acceptable product dioxins/furans concentration (in ng TEQ/kg product) is calculated using the CFIA standard for maximum acceptable 45-year cumulative dioxins/furans addition to soil (5.355mg TEQ/ha) and the product's maximum recommended annual application rate as follows:

Description
The maximum acceptable concentration of dioxins and furans in a product is equal to one million times the maximum acceptable cumulative addition of dioxins and furans to soil over 45 years divided by the product's annual application rate times 45.
In addition, a maximum product concentration of 100 ng TEQ/kg product is being considered to protect workers and bystanders. Table 4 shows the dioxin/furan acceptable concentrations for products at different application rates.
Maximum Acceptable Cumulative PCDD/F Additions to Soil over 45 Years (mg TEQ/ha) | Examples of Maximum Acceptable PCDD/F Concentration Based on Annual Application Rates (ng TEQ/ha) 4400 kg/ha - yr | Examples of Maximum Acceptable PCDD/F Concentration Based on Annual Application Rates (ng TEQ/ha) 2000 kg/ha - yr | |
---|---|---|---|
PCDD/F | 5.355 | 27 | 59.5 |
A compliance verification tool mentioned above (below Table 1) is available from paso-bpdpm@inspection.gc.ca upon request. The calculator includes functionality for Persistent Organic Pollutants limits.
Indicator Organisms
Monitoring for microbial contaminants in fertilizers and supplements must be carried out to provide information on the adequacy of pathogen-reducing processing or sterilization steps and the microbial condition of the final product. Given their widespread presence in the environment, Salmonella and Faecal coliform density are used as indicators of microbial contamination and effectiveness of treatment process, a practice aligned with the United States Environmental Protection Agency's Part 503 Rule. The requirement of indicator organism testing allows for detection of any regrowth of bacteria and substantiates the sufficiency of pathogen reduction processes in place.
Indicator Organism | Level | Minimum Detection Limit |
---|---|---|
Salmonella | Not Detectable | less than 1 CFU (Colony Forming Unit)/25 grams |
Faecal Coliforms | 1000 MPN (Most Probable Number)/ gram | less than 2 CFU/gram |
Tests for indicator organisms are required to meet the minimum detection limits specified in Table 5.
A compliance verification tool mentioned above (below Table 1) is available from paso-bpdpm@inspection.gc.ca upon request. The calculator includes functionality for indicator organism limits.
The CFIA reserves the right to require analyses for additional pathogenic organisms depending on the nature of the product, as assessed on a case-by-case basis.
Please refer to Health Canada's Compendium for Microbiological Analysis for examples of standard methods. To be accepted, a method must be proven to be specific, selective, reliable, and accurate for the active ingredient in the formulated products.
Upper tolerances
To promote safe use and enable compliance verification both at the premarket assessment stage as well as marketplace monitoring and enforcement, upper tolerances for micronutrient guarantees have been established. The tolerances are based on analytical variability associated with product analysis and sampling error as well as attainability based on modern manufacturing practices.
Guarantee Range | Permissible Guarantee Exceedance |
---|---|
< 0.0033 | 0.0013 |
0.0033-0.0099 | 0.0040 |
0.010-0.032 | 0.010 |
0.033-0.099 | 0.031 |
0.10-0.32 | 0.077 |
0.33-0.99 | 0.23 |
1.0-3.2 | 0.60 |
3.3-9.99 | 1.0 |
≥ 10 | 10% of Guarantee |
Please note that the tolerances vary depending on the range of the micronutrient guaranteed – the tolerance is greater in the low range guarantee and smaller as the concentration in the product is higher. For example, a 0.24% Cu guarantee has a permissible exceedance of 0.077, for a maximum acceptable Cu content of 0.317%. On the upper end 11% Cu guarantee has a permissible exceedance of 10% of the guarantee, in this case 1.1%, for a maximum acceptable Cu content of 12.1%.
Appendix 4: Toxicological hazards characterization
Characteristic | |
---|---|
Ingredient | |
Chemical Abstract Number (CAS#) | |
Relative Concentration in final product |
Exposure Model Inputs | Hazard Criteria | Value | Reference(s) |
---|---|---|---|
Organic carbon partitioning coefficient (Koc) | |||
Log Octanol Water partitioning coefficient (Log Kow) | |||
Water Solubility at 25°C | |||
Vapour Pressure | |||
Persistence Air | ≥ 2 days | ||
Persistence Water | ≥ 6 months | ||
Persistence Soil | ≥ 6 months | ||
Persistence Sediment | ≥ 1 year | ||
Bioaccumulation, Bioconcentration, Biomagnification Factors | > 5000 |
Endpoint by Exposure Route | Hazard Criteria Table Note 11 | Test Organism | Term | Effect | Dose | Reference(s) |
---|---|---|---|---|---|---|
Oral Acute | LD50 ≤ 500 mg/kg bw | |||||
Oral Subchronic | LO(A)EL ≤ 90 mg/kg bw | |||||
Oral Subchronic | NO(A)EL ≤ 30 mg/kg bw | |||||
Oral Chronic | LO(A)EL ≤ 30 mg/kg bw | |||||
Oral Chronic | NO(A)EL ≤ 10 mg/kg bw | |||||
Dermal Acute | LD50 ≤ 500 mg/kg bw | |||||
Dermal Irritation/Sensitization | ||||||
Inhalation Acute | LD50 ≤ 1500 mg/m3 | |||||
Ocular Irritation | ||||||
Carcinogenicity | For each ingredient where there is indication of carcinogenicity proceed to Appendix 5. | Table Note 11 | ||||
Clastogenicity and Mutagenicity | For each ingredient where there is indication of clastogenicity or mutagenicity proceed to Appendix 5. | |||||
Reproductive/Developmental Toxicity, Teratogenicity | For each ingredient where there is indication of reproductive/developmental toxicity, teratogenicity proceed to Appendix 5. | |||||
Endocrine Disruption | For each ingredient where there is indication of endocrine disruption proceed to Appendix 5. |
Table Notes
- Table note 11
-
Cancer potency factor (q1*)
Category | Hazard Criteria Table Note 12 | Test Organism | Term | Effect | Concn | Reference(s) |
---|---|---|---|---|---|---|
Vertebrate (e.g. Rainbow trout (Oncorhynchus mykiss), Brook trout (Salvelinaus fontinalis), Fathead minnow (Pimephales promelas), Bluegill sunfish (Lepomis macrochirus)) | Acute: Lowest EC50 or LC50 < 0.1 ppm | |||||
Invertebrate (e.g. Daphnia (Daphnia sp., Ceriodaphnia dubia), Zebra fish (Brachydanio rerio), Worm (Lumbriculus variegatus)) | Acute: Lowest EC50 or LC50 < 0.1 ppm | |||||
Benthic (e.g. Amphipod (Hyallela azteca), Midge larvae (Chironomus tentans, Chironomus riparius)) | Acute: Lowest EC50 or LC50 < 0.1 ppm | |||||
Algae (e.g. Pseudokrchneriella subcapitata, Champia parvula) | Acute: Lowest EC50 or LC50 < 0.1 ppm |
Table Notes
- Table note 12
-
For each ingredient where any of the hazard criteria are met, proceed to Appendix 5
Appendix 5: Toxicological exposure and risk assessment
Only to be populated for high hazard ingredients (i.e. those that meet any of the Hazard Criteria identified in Appendix 4)
Mixer/Applicator
Assumption/Derivation/Rationale | |
---|---|
Application methodology/equipment | |
Application rate | |
Area of application (ha) | |
Frequency of application | |
Expected route(s) of exposure (e.g. dermal, inhalation) based on application method and product and constituent physico-chemical properties |
|
Mitigative Factors Limiting Exposure | |
Personal Protective Equipment (PPE) | |
Dermal Absorption Factor (if applicable) (% of oral dose) (DAF) | Provide value and associated reference |
Estimate of exposure, A (mg/kg bw/d) | Show derivation and associated modelling assumptions |
Assumption/Derivation/Rationale | |
---|---|
Critical endpoint and critical, B (mg/kg bw/d) and/or Cancer potency factor, q1* (mg/kg bw/d)-1 |
As identified in Appendix 4 |
Margin of Safety (B/A) and/or Incremental Lifetime Cancer Risk (ILCR) (q1* x A) |
Bystander/Indirect
Assumption/Derivation/Rationale | |
---|---|
Method of exposure (e.g. drift, re-entry, soil contact or consumption, potable water, plant residues) |
|
Application rate | |
Area of application | |
Frequency of exposure | |
Application setting (e.g. agriculture, greenhouse, residential) | |
Re-entry Interval | |
Expected route(s) of exposure (e.g. dermal, inhalation) based on application method and product and constituent physico-chemical properties |
|
Environmental media concentration (ppm) (as required) | Exceedance of persistence screening criteria (Appendix 4) must be accounted for in this derivation |
Estimate of exposure, A (mg/kg bw/d) | Show derivation, identify model used and associated modelling assumptions |
Assumption/Derivation/Rationale | |
---|---|
Critical endpoint dose, B (mg/kg bw/d) and/or Cancer potency factor, q1* (mg/kg bw/d)-1 |
As identified in Appendix 4 |
Margin of Safety (B/A) and/or Incremental Lifetime Cancer Risk (ILCR) (q1* x A) |
Environmental
Assumption/Derivation/Rationale | |
---|---|
Expected target environmental media (e.g. soil, air, aquatic, sediment) based on application method and product and constituent physico-chemical properties |
|
Application methodology/equipment | |
Application rate | |
Frequency of application | |
Environmental media concentration estimate, C (ppm) (e.g. impregnated granule, soil, sediment or aquatic concentration) |
Show derivation, identify model used and associated modelling assumptions Exceedance of persistence and/or biomagnification/bioaccumulation/ bioconcentration screening criteria (Appendix 4) must be accounted for in this derivation |
Organism(s) of concern exposure estimate(s), D (mg/kg bw/d) (if applicable, e.g. avian/terrestrial vertebrate toxicity) |
Show derivation, identify model used and associated assumptions (e.g. daily soil/granule ingestion rate) |
Assumption/Derivation/Rationale | |
---|---|
Organism(s) of concern and associated critical environmental concentration(s), E (ppm) | As identified in Appendix 4 |
Organism(s) of concern and associated critical dose, F (mg/kg bw/d) (if applicable e.g. avian/terrestrial vertebrate toxicity) |
As identified in Appendix 4 |
Risk Quotient (E/C) | |
Margin of Safety (F/D) (if applicable e.g. avian/terrestrial vertebrate toxicity) |
B The critical effect is typically the first adverse effect that occurs with increasing dose; the critical dose is the dose at which this adverse effect is observed.
The carcinogenic potency factor (q1*) is a measure of the relative strength of a non-threshold carcinogen.
Appendix 6: Microbial hazard characterization (checklist)
Organism | Hazard | Yes/No | References |
---|---|---|---|
Human | Pathogenicity/Toxicity | ||
Human | Sensitization/Irritation | ||
Human | Dermatophytic potential | ||
Human | Toxigenicity Table Note 13 | ||
Mammals | Pathogenicity/Toxicity | ||
Mammals | Sensitization/Irritation | ||
Mammals | Dermatophytic potential | ||
Mammals | Toxigenicity Table Note 13 | ||
Other terrestrial vertebrates (e.g. birds) | Pathogenicity/Toxicity | ||
Other terrestrial vertebrates (e.g. birds) | Sensitization/Irritation | ||
Other terrestrial vertebrates (e.g. birds) | Toxigenicity Table Note 13 | ||
Terrestrial plants/crops | Pathogenicity/Toxicity | ||
Terrestrial plants/crops | Growth inhibition | ||
Terrestrial plants/crops | Post-harvest spoilage | ||
Terrestrial invertebrates (e.g. bees, earthworms, springtails) | Pathogenicity/Toxicity | ||
Aquatic vertebrates (fishes) | Pathogenicity/Toxicity | ||
Aquatic invertebrates (benthic, epibenthic) | Pathogenicity/Toxicity | ||
Aquatic plants (algae) | Pathogenicity/Toxicity |
Table Notes
- Table note 13
-
Hazard to a toxin can be estimated using established chemical models (see Appendix 4)
Appendix 7: Microbial exposure characterization - factors to consider
Category | References |
---|---|
Geographical distribution | |
Natural habitats: soils, water, atmosphere, on or inside of living organisms (e.g. endophyte, epiphyte) | |
Hosts (symbiotic, saprophytic or pathogenic relationships) | |
Food/feed crops on which the microorganism is found in nature | |
Residues on food/feed (accumulation of the microorganism or its metabolites in the edible portion of the plant) Table Note 14 |
Table Notes
- Table Note 14
-
Residue data are used to estimate the dietary exposure of humans and livestock to microbial toxins.
Category | References |
---|---|
Growth parameters (e.g. temperature, pH, osmotic minima, maxima and optima) | |
Nutritional dependence, oxygen requirements, energy sources | |
Susceptibility to antibiotics, metals and environmental factors such as sunlight and desiccation | |
Favorable conditions for toxin production Table Note 15 |
Table Notes
- Table Note 15
-
Exposure to a toxin can be estimated using established chemical models (see Appendix 5).
Category | References |
---|---|
Characteristics of the different forms of the microorganism during its life cycle (e.g. motile cells, dormant cysts, spores) | |
Mechanism for reproduction and dispersal | |
Mechanism for survival (in adverse conditions) | |
Potential for dispersal of traits or gene transfer (mandatory for microorganisms modified by molecular biological techniques) |
Category | References |
---|---|
Unusual properties of the notified strain that differ from the classical description of the species (mandatory for microorganisms modified by molecular biological techniques) |
Category | References |
---|---|
Crops/plants on which the product is intended to be used | Label |
Application methodology/equipment | Label |
Application rate | Label |
Frequency of application | Label |
Expected route(s) of exposure (e.g. dermal, inhalation, ingestion) |
Appendix 8: Considerations for classification of microbial hazard severity and exposure level
Classification | Considerations for classification Hazard Severity | Considerations for classification Exposure Level |
---|---|---|
High |
|
|
Medium |
|
|
Low |
|
|
Source: Adapted from Environment Canada and Health Canada (2011): Framework for Science-Based Risk Assessment of Micro-Organisms Regulated under the Canadian Environmental Protection Act, 1999
Note: Combinations of the factors within each generalized hazard severity or exposure level above are possible and would affect the overall hazard or exposure assessment.
Appendix 9: Labelling requirements for fertilizer-pesticides permitted for home and garden uses
Common Name: Table Note 17 | Corn gluten meal |
---|---|
Guaranteed analysis: Table Note 16 Table Note 17 | Corn gluten meal (actual) Table Note 16 |
Approved For Use: Table Note 17 | In specialty lawn/turf fertilizers containing compatible fertilizer constituent materials. |
Approved Claims: Table Note 16 Table Note 17 | Pre-emergence inhibition of large and smooth crabgrass, white clover and dandelion seed germination in residential lawns where established perennial ryegrass or established Kentucky bluegrass are the predominant grass species. Pre-emergence inhibition of large crabgrass, white clover and dandelion seed germination in public areas such as sports fields, parks, golf areas, and sod farms, where established perennial ryegrass or established Kentucky bluegrass are the predominant grass species. |
Application Rates: Table Note 16 Table Note 17 | 9500 - 9800 g of corn gluten meal / 100m2 |
Directions For Use: Table Note 16 Table Note 17 | May inhibit weed seed germination when used in conjunction with a sound lawn (or turf) maintenance program. Table Note 16 Established weeds at time of application will not be inhibited. Table Note 16 Do not apply the product on newly seeded grass as it may inhibit seeds from germinating, wait until after first mowing when root systems are established. Table Note 16 If over-seeding or re-sodding in the spring, do not apply the product in the spring. If over-seeding or re-sodding in the fall, do not apply the product in the fall. Table Note 16 For best results: Apply to established turf twice a year; once in the early spring 2 weeks before weed seed germination, and once in the late summer or early fall after heat stress has passed. Table Note 16 Apply when soil is moist and when rain is forecasted within 2 days of treatment. If rainfall does not occur within 2 days of treatment, irrigation is required. Excessive moisture at time of treatment may reduce the effectiveness of the product. Table Note 16 Do not apply under windy conditions. Product application dates may vary for both the spring and late summer/early fall application from year to year according to weather conditions. The inhibitory effect of the product to weed seeds generally dissipates in five weeks following application. Apply to a mature lawn having a well-developed root mass. Large crabgrass seeds germinate when soil temperature reaches 12.8°C. |
Precautions: Table Note 16 Table Note 17 | Keep Out Of Reach Of Children [On Main And Secondary Panels]. Table Note 16 Table Note 17 Read The Label Before Using [On Main Panel]. Table Note 16 Table Note 17 Caution Eye Irritant [On Main Panel]. Table Note 16 Table Note 17 Potential Sensitizer [On Main Panel]. Table Note 16 Table Note 17 May cause sensitization. Table Note 16 Avoid contact with skin, eyes or clothing. Table Note 16 Avoid inhaling dusts. Table Note 16 For good hygiene practice, wear a long-sleeved shirt, long pants, closed footwear and gloves when handling the product. Table Note 16 It is recommended that a dust mask be worn when transferring the product to the spreader. Table Note 16 Should not be applied if the applicator or a member of the household has a sensitivity or allergy to corn. Table Note 16 |
First Aid: Table Note 16 Table Note 17 | If Swallowed: Table Note 16 Table Note 17 Rinse mouth and throat with copious amounts of water. Do not induce vomiting. Table Note 16 If On Skin/Clothing: Table Note 16 Table Note 17 Take off contaminated clothing. Wash skin with plenty of soap and water. Table Note 16 If Inhaled: Table Note 16 Table Note 17 Move to fresh air. Table Note 16 If In Eyes: Table Note 16 Table Note 17 Hold eye open and rinse slowly and gently with water. Remove contact lenses if present, then continue rinsing eye. Table Note 16 General: Table Note 16 Table Note 17 Seek medical attention immediately if irritation or signs of toxicity occur and persist or is severe. Take container, label or product name and registration number with you when seeking medical attention. Table Note 16 |
Toxicological Information: Table Note 16 Table Note 17 | Treat symptomatically. Table Note 16 |
Storage: Table Note 16 Table Note 17 | Keep in cool, dry conditions, away from seed, fertilizer and other pesticides. Keep away from fire, open flame, or other sources of heat. Table Note 16 |
Disposal: Table Note 16 Table Note 17 | Do not re-use empty container. Dispose in accordance with municipal or provincial regulations if applicable. If no such regulations apply, wrap and dispose of empty container with household garbage. |
Notice To User: Table Note 16 Table Note 17 | This product is to be used in accordance with the directions on this label. It is an offence under the Pest Control Products Act to use this product under unsafe conditions. |
Accepted Compatible Pesticide Active Ingredients: Table Note 17 | None |
Approved Brands Of Pesticide Products: Table Note 17 | Refer to the corn gluten meal section PMRA's approved brands of pesticide products |
Table Notes
- Table note 16
-
The headings or statements must appear on the label. Note: The other statements are recommended but not required.
- Table note 17
-
Must be capitalized on the label unless otherwise indicated.
Note: The exact wording of all statements is encouraged but not mandatory as long as the meaning is the same. No contradictory information may appear on the label.
Note: Text in square brackets [ ] is additional information and should not be included on the label.
Common Name: Table Note 19 | FERROUS SULPHATE Table Note 19 |
---|---|
Guaranteed Analysis: Table Note 18 Table Note 19 | Ferrous Sulphate (actual) Table Note 18 |
Approved For Use: Table Note 19 | In specialty lawn/turf fertilizers containing compatible fertilizer constituent materials. |
Approved Claims: Table Note 18 Table Note 19 | Controls moss in lawns. |
Application Rates: Table Note 18 Table Note 19 | 250 - 980 g of Ferrous sulphate / 100m2 |
Directions For Use: Table Note 18 Table Note 19 | In lawns: Moss will take over under conditions of poor light, poor drainage and inadequate plant food. Prune trees to open up and reduce shade. Improve drainage with tiling, slit trenching or contouring. Fertilize on a regular basis. For immediate control of moss water lawn thoroughly. Spray on recommended rate. Water in to wash off grass blades; then with-hold water for several days. May also be applied at dry rate, but water in thoroughly immediately after application. |
Precautions: Table Note 18 Table Note 19 | KEEP OUT OF REACH OF CHILDREN. Table Note 18 Table Note 19 READ LABEL BEFORE USING [on main panel]. Table Note 18 Table Note 19 Harmful if swallowed. Table Note 18 Avoid contact with eyes, skin and clothing. Table Note 18 Avoid breathing dust or spray mist. Table Note 18 Store in its original container tightly closed and away from children and pets. Table Note 18 Wash hands after use. May stain stone, brick masonry or light coloured sidings. May corrode bare metal. Flush off spills with clear water. Do not use on cement products such as sidewalks, patios, blocks, stucco, etc. |
First Aid: Table Note 18 Table Note 19 | If Swallowed: Table Note 19 Get medical attention or contact poison control centre. If In Eyes: Table Note 19 Flush with plenty of water and get medical attention or contact poison control centre. If On Skin: Table Note 19 Wash with soap and water. Table Note 18 |
Disposal: Table Note 18 Table Note 19 | Discard empty container in household garbage. |
Accepted Compatible Pesticide Active Ingredients: Table Note 19 | None |
Approved Brands Of Pesticide Products: Table Note 19 | Refer to the ferrous sulphate section PMRA's approved brands of pesticide products |
Table Notes
- Table note 18
-
The headings or statements must appear on the label. Note: The other statements are recommended but not required.
- Table note 19
-
Must be capitalized on the label unless otherwise indicated.
Note: The exact wording of all statements is encouraged but not mandatory as long as the meaning is the same. No contradictory information may appear on the label.
Note: Text in square brackets [ ] is additional information and should not be included on the label.
Appendix 10: Information resources - toxicology
Canadian Resources
Canadian Centre for Occupational Heal and Safety (CCOHS)
1. CCOHS: http://ccinfoweb.ccohs.ca/
Committee on Standards, Equity, health and safety at work (CNESST)
2. Repository Toxicology: http://www.csst.qc.ca/en/prevention/reptox/Pages/to-english-users.aspx
Environment Canada
3. Domestic substances list: https://www.canada.ca/en/environment-climate-change/services/canadian-environmental-protection-act-registry/substances-list/domestic.html
Health Canada
4. First Priority Substances List (PSL1) Assessments: http://www.hc-sc.gc.ca/ewh-semt/pubs/contaminants/psl1-lsp1/index_e.html
5. Second Priority Substances List (PSL2): Assessments http://www.hc-sc.gc.ca/ewh-semt/pubs/contaminants/psl2-lsp2/index_e.html
International Resources
Australian Government
6. Department of Health, National Industrial Chemicals, Notification and Assessment Scheme, Priority Existing Chemical Assessments: https://www.nicnas.gov.au/chemical-information/pec-assessments
United Nations
7. Food and Agriculture Organization (FAO), The Codex Alimentarius: http://www.fao.org/faostat/en/#home
8. International Programme on Chemical Safety (IPCS) INCHEM: http://www.inchem.org/
United States
9. Agency for Toxic Substances and Disease Registry (ATSDR), Toxic Substances Portal: https://www.atsdr.cdc.gov/
10. Centers for Disease Control and Prevention (CDC), The National Institute for Occupational Safety and Health (NIOSH): https://www.cdc.gov/niosh/npg/npgsyn-a.html
11. Department of Commerce, National Institute of Standards and Technology (NIST), NIST Chemical WebBook, SRD 69: http://webbook.nist.gov/chemistry/name-ser/
12. Environmental Protection Agency (EPA), Ecotox: http://cfpub.epa.gov/ecotox/
13. Environmental Protection Agency (EPA), Integrated Risk Information System https://www.epa.gov/iris
14. National Library of Medicine, Toxicological Data Network: ChemIDplus https://chem.nlm.nih.gov/chemidplus/
Appendix 11: Information resources - microbiology
Canadian Departments/Agencies
Canadian Food Inspection Agency (CFIA)
2. Plant Pests regulated by Canada
Environment Canada
3. Environment Canada and Health Canada. 2011. Framework for Science-Based Risk Assessment of Micro-Organisms Regulated under the Canadian Environmental Protection Act, 1999.
4. Environment Canada, Report EPS 1/RM/44. March 2004. Guidance document for testing the pathogenicity and toxicity of new microbial substances to aquatic and terrestrial organisms.
5. Environment Canada, Report EPS 1/RM/46. March 2005 (with June 2007 amendments). Guidance document on statistical Methods for Environmental Toxicity Tests.
6. Environment Canada. December 2013. Organisms on the Domestic Substances List (DSL) (Contains several risk group 2 microorganisms).
Health Canada/Public Health Agency of Canada
7. Human pathogen list: Chapter 2 of the Health Canada Laboratory Biosafety Guidelines provided a list of infectious agents by Risk Group. For questions about the Risk Group classification of specific organisms, please contact the Office of Laboratory Security.
8. Non-pathogenic organisms that do not require permit to import into Canada
International Resources
American Type Culture Collection (ATCC)
9. Cultures from the ATCC Bacteriology Collection
OECD (Organisation for Economic Co-operation and Development)
10. OECD (Organisation for Economic Co-operation and Development). 1998a. Principles of Good Laboratory Practice (as revised in 1997), No 1 - OECD Series on Principles of Good Laboratory Practice and Compliance Monitoring, ENV/MC/CHEM(98)17, 41 p., Environment Directorate, Paris, France.
11. OECD (Organisation for Economic Co-operation and Development). 1999d. The application of the GLP principles to Short Term Studies, No 7 (revised) - OECD Series on Principles of Good Laboratory Practice and Compliance Monitoring, ENV/JM/MONO(99)23, 16 p., Environment Directorate, Paris, France.