Cleaning and disinfection (C&D) is performed on premises declared infected to ensure the site (including areas that animals have occupied, materials, equipment and other items identified as contaminated) does not pose a risk for the transmission of a federally reportable disease.
Responsibility
On premises that have been issued a Declaration of an Infected Place (CFIA/ACIA form 4204), cleaning and disinfection is required. The CFIA C&D Unit will conduct an assessment of the premises to determine the degree of contamination and risk of transmission of bovine tuberculosis. The CFIA will develop a decontamination plan and issue the owner of the premises an Order to Clean and Disinfect (CFIA/ACIA form 4207), reviewing with the owner the requirements of the plan.
The owner will conduct the C&D under the approval and oversight of the CFIA.
The CFIA oversees the C&D of the premises, conducting a minimum of three site visits. When cleaning and disinfection is completed to the satisfaction of the CFIA, a signed declaration is provided indicating approval of the process. The premises remains under CFIA control until a Declaration That a Premises Has Ceased to Be an Infected Place (CFIA/ACIA form 4205) is issued.
Important considerations
- Under the federal Health of Animals Act and Regulations, producers are not eligible for compensation from the CFIA for the costs of C&D. Producers may be eligible for financial assistance through specific event initiatives under the Agri-Recovery framework.
- The pathogen Mycobacterium bovis (M. bovis) that causes bovine tuberculosis can occasionally cause disease in humans. While human infections are rare, minimizing potential exposure to the pathogen is important. Some measures to reduce exposure and transmission include minimizing aerosolization of dust particles during C&D. In dry conditions, consideration may be given to lightly wetting down material and during the wet cleaning when using power washers, using low pressure spray. Producers are advised to seek guidance from their health care professional on the risks and measures to minimize disease exposure.
Background
The pathogen that causes bovine tuberculosis can be shed by infected animals in their respiratory secretions, sputum, feces, urine, vaginal and uterine discharges and other bodily fluids. The pathogen can survive for long periods of time in cool temperatures in organic material such as manure and in water dugouts.
Process
Cleaning and Disinfection normally involves 6 (six) steps:
While the process for C&D is similar for all infected premises, the specific requirements and needs must be tailored to address the disease risks and issues specific to each premises. In some circumstances not all six steps will be required.
Step 1: Removal of contaminated materials and products
This step covers the removal of contaminated materials and products not suitable for cleaning and disinfection and their proper disposal.
(Consult the CFIA Disposal Unit for guidance on disposal of contaminated material or things)
- Remove contaminated materials (such as scrap lumber, pallets, cardboard boxes, etc.) that are not suitable for C&D to a location designated by the CFIA Disposal Unit. Disposal of the materials may include burning, burial or other methods as approved by the CFIA Disposal Unit.
- Remove accumulations of manure, used bedding, and other organic material for treatment and or disposal to a location on the premises as directed by the CFIA Disposal and C&D Units.
- Remove equipment and materials that can be C&D to an appropriate location on the premises as approved by the CFIA C&D Unit. When cleaning buildings, pens and large equipment, there may be items that can be cleaned and disinfected, yet interfere with cleaning and disinfecting of the location. For example, in pens: feeders, waterers, halters, pitchforks, shovels, wheel barrows, buckets, bottles and other items should be cleaned and disinfected and moved to a "clean" area on the premises or moved to a location on the premises and cleaned and disinfected.
Step 2: Dry cleaning
This step covers the dry cleaning of surfaces (using shovels, scrapers, brushes, etc.) to remove gross organic material.
Dry cleaning is the most important step in the C&D process; it removes the largest amount of infectious (contaminated) material containing the pathogen (Mycobacterium bovis) and when performed correctly, reduces the amount of work required for wet cleaning.
- Organic material must be removed from surfaces such as walls, fences, rails, etc., (particularly from the areas animals have occupied) as it will inactivate disinfectants and render disinfection procedures ineffective. Any equipment in those areas subject to the same protocol (e.g. water troughs, hay feeders, tractors, manure spreaders, etc.).
- Removal of used bedding and contaminated feed for appropriate treatment/disposal.
- Removal of manure piles and manure present on the ground for appropriate treatment and disposal.
- Removal of 2.5 cm of soil from the areas where animals congregated in pens or corrals; consider areas on pasture that have a high volume of animal congregations such as water sources, salt licks, etc.).
Step 3: Wet cleaning
This step covers the wet cleaning of surfaces (using soaps, detergents, or products such as enzymes) to further remove gross organic material and biofilms.
- Use of soaps, detergents, or enzymatic cleaners for the removal of biofilms and organic material if still present. Flaming or burning of surfaces for removal and inactivation of biofilms and organic material (if still present) that are not amenable to wet cleaning (e.g. wood, packed clay, etc.) or when climatic conditions (e.g. freezing temperatures) interfere with the process.
Step 4: Drying (post cleaning)
This step covers the drying of surfaces (this may include the use of supplemental heat in buildings)
- Allow all surfaces to thoroughly dry as this assists in inactivating the pathogen (M. bovis).
Contact the CFIA for approval of the cleaning process.
An inspection is required before beginning the disinfection process.
Step 5: Disinfection
This step covers the disinfection of surfaces (using a chemical disinfectant registered and approved for that purpose) or other suitable method/physical process to inactivate the agent of concern. (e.g. heat treatment through flaming or burning)
- The use of a chemical disinfectant registered in Canada and approved for use as being effective against M. bovis is required. Alternatively, any other method (physical disinfection process) that provides adequate inactivation of the pathogen can be applied to surfaces if suitable (e.g. heat / flame or exposure to sunlight [ultraviolet light] and drying).
- Since the disinfection of wood is difficult to achieve, it is advised that wood surfaces should be sealed/painted as part of the disinfection process. Wood may also be treated with moist or dry heat (surface burned).
Contact the CFIA for the supervision and approval of the disinfection process.
Step 6: Drying (post disinfection)
This step covers the drying of surfaces (this may include the use of supplemental heat on equipment or in buildings)
- Allow all surfaces to thoroughly dry as this assists in inactivating the pathogen (M. bovis).
- A vacant period/downtime (when no animals are present on the premises) is required prior to restocking. The removal of a susceptible host species helps minimize opportunity for survival of the pathogen, reinfection of a susceptible animal and multiplication of the pathogen. The length of time required for this vacant period may vary given such factors as environmental conditions suitable to pathogen survival and levels of infection on the premises.
Overview of the Cleaning and Disinfection Process
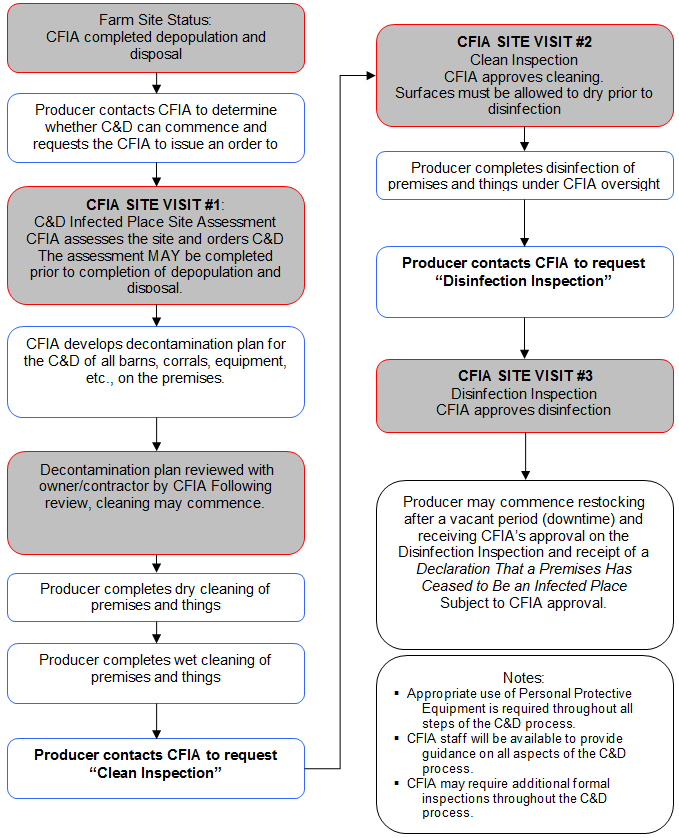
Description of flowchart - Overview of the Cleaning and Disinfection Process
- Farm Site Status: CFIA completed depopulation and disposal
- Producer contacts CFIA to determine whether C&D can commence and requests the CFIA to issue an order to C&D.
- CFIA site visit #1: C&D Infected Place Site Assessment CFIA assesses the site and orders C&D. The assessment MAY be completed prior to completion of depopulation and disposal.
- CFIA develops decontamination plan for the C&D of all barns, corrals, equipment, etc., on the premises.
- Decontamination plan reviewed with owner/contractor by CFIA Following review, , cleaning may commence.
- Producer completes dry cleaning of premises and things.
- Producer completes wet cleaning of premises and things.
- Producer contacts CFIA to request "Clean Inspection"
- CFIA site visit #2: Clean Inspection CFIA approves cleaning. Surfaces must be allowed to dry prior to disinfection.
- Producer completes disinfection of premises and things under CFIA oversight.
- Producer contacts CFIA to request "Disinfection Inspection"
- CFIA site visit #3: Disinfection Inspection CFIA approves disinfection
- Producer may commence restocking after a vacant period (downtime) and receiving CFIA's approval on the Disinfection Inspection and receipt of a Declaration That a Premises Has Ceased to Be an Infected Place Subject to CFIA approval.
Notes:
- Appropriate use of Personal Protective Equipment is required throughout all steps of the C&D process.
- CFIA staff will be available to provide guidance on all aspects of the C&D process.
- CFIA may require additional formal inspections throughout the C&D process.
Examples of approved disinfectants
- LpH ag® manufactured by Steris
Follow label directions of the disinfectant. Mix one part of disinfectant to 250 parts of water. - Sodium hypochlorite
Household bleach concentration is generally 5-6%. For Tuberculosis, it is recommended a dilution of 1 part of bleach and 4 parts of water (1/5 solution). - PREvailTM (accelerated hydrogen peroxide) manufactured by Virox
Follow label directions of the disinfectant. Consideration of using 1/16 dilution and 10-20 minutes contact time in cold weather.
To make 1 litre for use at: | Water Table Note 1 | Calcium Chloride | Accel Prevention Concentrate 7%Table Note 2 |
---|---|---|---|
0 to -20°Celsius | 800 ml (+) | 200 g | 63 ml |
Table Notes
- Table Note 1
-
Add CaCl2 to water and mix until dissolved. The solution will warm up to ~ 40 °C. Then add the Accel and finally top up to 1 litre with more water.
- Table Note 2
-
A cloudy precipitate may form and settle out of solution. This is expected. Allow to settle and then pour into the final container for use. As well, a very slight chlorine smell may develop over time. This also is normal.
Contact time required: a minimum of 10 minutes under ideal conditions. During cold temperatures, increased contact time will be required. Discuss requirements with the CFIA C&D Unit.
Product | Format | Order number |
---|---|---|
Xynyth Calcium Chloride 94-97% | 50kg | Acklands Grainger # XYN200-50049 |
Calcium Chloride | 3kg | Fisher Scientific C6143 |
To make 1 litre for use at: | Water | Propylene glycol | Accel Prevention Concentrate 7% |
---|---|---|---|
0 to -10°Celsius | 637 ml | 300 ml | 63 ml |
-10 to -20°Celsius | 537 ml | 400 ml | 63 ml |
Discuss requirements with the CFIA C&D Unit.
Product | Format | Supplier - Order number |
---|---|---|
Propylene Glycol | 18.9L | Hall-Chem Table Note 3 PG300-19 |
Prestone Plumbing/RV Antifreeze Table Note 4 | 4L | Canadian Tire #63-9926-4 |
Propylene Glycol USP/FCC | 4 Litres | Fisher Scientific - P3554 |
Table Notes
- Table Note 3
-
Hall-Chem is an importer/packager of PG for retail. They can arrange 3.8L production lots and bulk shipping
- Table Note 4
-
Do not substitute other commercial antifreezes without verifying additives will not interfere with the disinfectant.